By Greg Force, Chief Executive Officer
Additives to concrete mixes to improve workability, as well as to maintain high early strengths while limiting water demand, have been researched for decades. Fly ash was the subject of a study undertaken in 1990, which showed benefits via field applications that have prompted widespread use within the industry ever since. Studies were later done in specific product applications where the density of the matrix was augmented by adding silica fume, thereby increasing strength and the chloride and moisture penetration resistance.
Work refining the matrix of cementitious materials has continued over the last twenty-five years. This refined matrix in combination with fiber reinforcement, has led to modern UHPC, which has high compressive strength, extensive durability, and, perhaps most significantly, high tensile strength and post-cracking ductility. To date, UHPC has seen limited commercial use, such as for thin shells for architectural applications and in deck connections for the transportation sector. These projects have typically involved material of a proprietary nature.
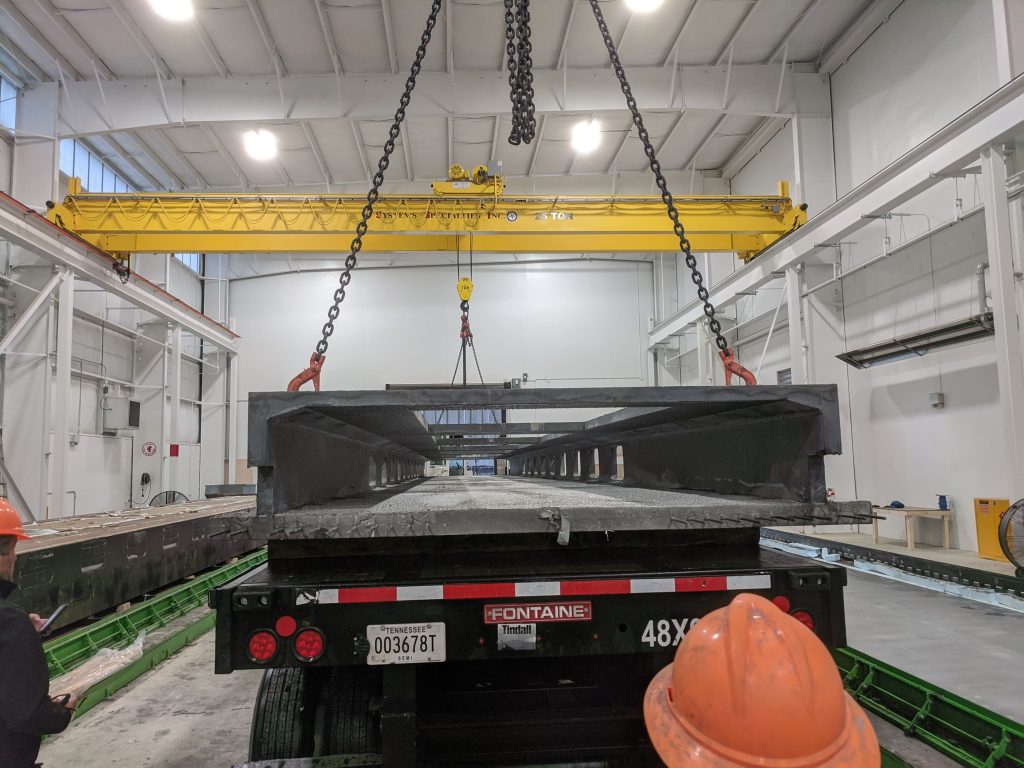
In the NOV-DEC 2016 issue of PCI Journal, Geisler, Applegate, and Weldon presented a paper entitled, “Implementing Non-proprietary Ultra-High-Performance-Concrete in a Precasting Plant,” which was partially funded by a PCI Jenny Fellowship and by the New Mexico Department of Transportation. The study successfully showed that concrete capable of achieving high compressive strengths on the order of what would be considered UHPC could be produced by adapting laboratory methods on a large scale with no significant changes to the plant facilities. Additionally, it showed that locally available materials could be utilized to produce this concrete.
The work noted above, plus research by other entities, led to a major industry-funded project on Ultra-High-Performance Concrete (UHPC), which took place between 2018 and 2021 and in which Tindall was one of the six producer participants. The focus of this research was two-fold. The first objective was to facilitate the implementation of UHPC materials. This involved proving that consistent production of concrete mixes with compressive strength of 18,000 psi (124 MPa) and tensile strength of 1700 psi (12 MPa) using regionally available materials was feasible. Providing such an alternative to bagged materials with costs per cubic yard under $1,000 would presumably make its commercial application all the more attractive. This work also produced material and quality control guidelines and a draft specification. Of necessity, this study was limited to steel fibers of a certain size and the target design strengths rather than a broader, more encompassing study.
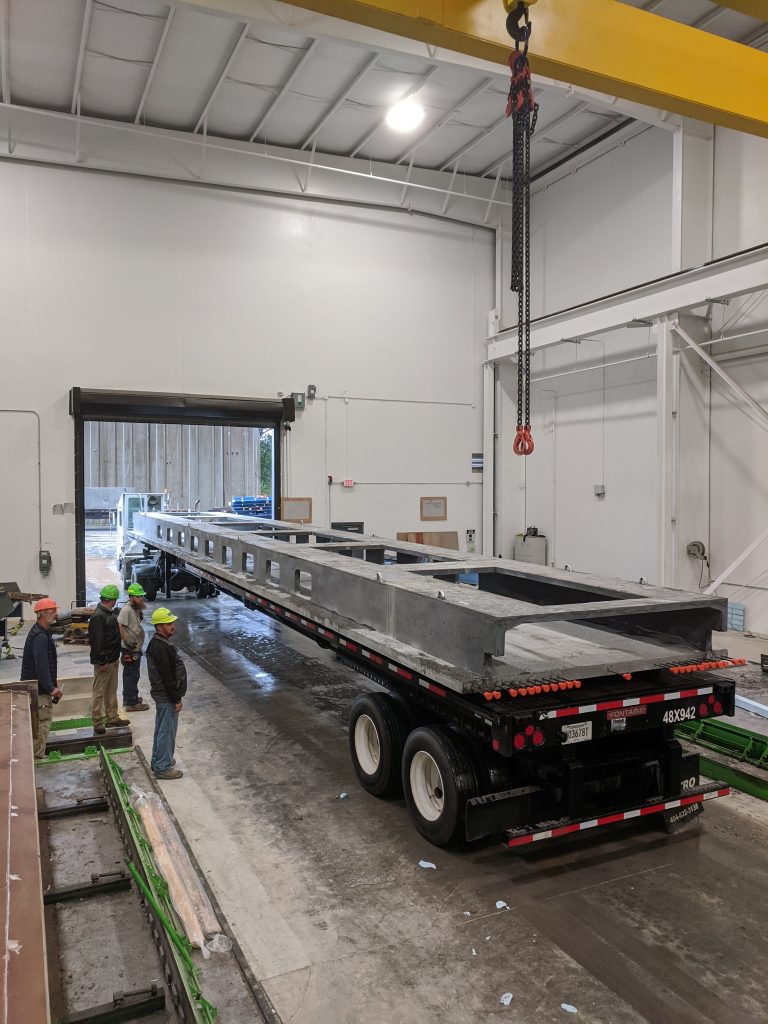
The second objective of the research was to define design parameters for use in flexural elements, both for transportation and for building applications, seeking to optimize member cross section by gaining maximum benefit of the material properties. Tindall undertook the design and manufacture of a voided floor slab, which performed well under testing but, unfortunately, wasn’t very efficient to produce. While the right application for such a floor member has not yet been identified, it is worth noting that a precaster in the upper Midwest recently completed a multi-story commercial project using UHPC to create voided box beams with openings in the sides to support floor elements and allow penetrations to accommodate ductwork, conduit, and piping. Perhaps the greatest significance of this application was the ability to virtually double the span of the originally designed steel beams by using this member, weighing roughly half what a normal concrete beam would weigh, without sacrificing available headroom. For a building’s space utilization, functionality, and future flexibility, this checks all the boxes. Sustainability is further enhanced by cement reduction through more efficient mix designs or through efficient and smaller cross sections needing significantly less volume.
Tindall’s participation in the PCI research project has allowed us to continue learning about this exciting material, and we are actively seeking new opportunities for its beneficial use. One current research project looks to extrapolate the findings of the PCI program and apply them to lower-strength mixes utilizing non-metallic fibers suitable for architectural applications. If you should have an upcoming project for which this type of innovative thinking could be a game-changer, give us a call because Tindall is Engineered to Serve!
This post is based on an article that originally appeared in the September-October 2023 issue of the PCI Journal. Revised by the author and used with permission.