In the construction world, innovation and efficiency are the cornerstones of success. Architects and builders are constantly on the lookout for construction methods and materials that can deliver faster and higher quality outcomes. Amid this pursuit, precast concrete has emerged as a standout choice for many, boasting a level of versatility and strength that few materials can match. But what exactly is precast concrete, and what sets it apart from traditional construction methods?
In this article, we will examine precast concrete construction. We’ll discuss what precast is specifically, the intricacies of how it’s manufactured, and the multitude of applications and advantages it brings to the table. Whether you are a planner, a developer, a designer, or simply a construction enthusiast, it’s important to know why precast has become such a game-changer in the construction industry.
What Is Precast Concrete?
Precast concrete is a high-performing construction material manufactured in controlled environments away from its final position. Unlike traditional cast-in-place concrete, precast concrete is produced in controlled conditions, often in a manufacturing facility that adheres to exceptional quality control standards. In this factory setting, the concrete mixture, curing conditions, and attributes like dimensional tolerance are closely monitored through numerous quality checks and testing. The result? Consistent, higher-quality construction elements with fewer defects and variations when compared to cast-in-place concrete. Uniform concrete elements reduce waste, lower costs, and allow for the construction of more resilient, longer-lasting final products and structures.
How Is Precast Concrete Made?
The manufacturing process of precast concrete begins with meticulous mold preparation or as precast manufacturers refer to it, “form building.” These reusable molds or forms are made from durable materials like steel or wood and crafted to accommodate multiple pouring cycles. Reinforcement is typically placed within the forms to add strength and control cracking. Steel lifters and connection plates are also placed within the forms to allow for lifting the pieces during erection and joining the parts together. Each precast piece is thoughtfully designed early on to meet a project’s precise requirements while also aiding efficient manufacturing. The versatility of precast concrete shines through this process as the forms can be adapted and customized to accommodate a wide array of shapes and designs. Whether they are architectural and ornate or structural elements, such as wall panels, slabs, columns, and beams, precision forming plays a vital role in bringing these elements to life.
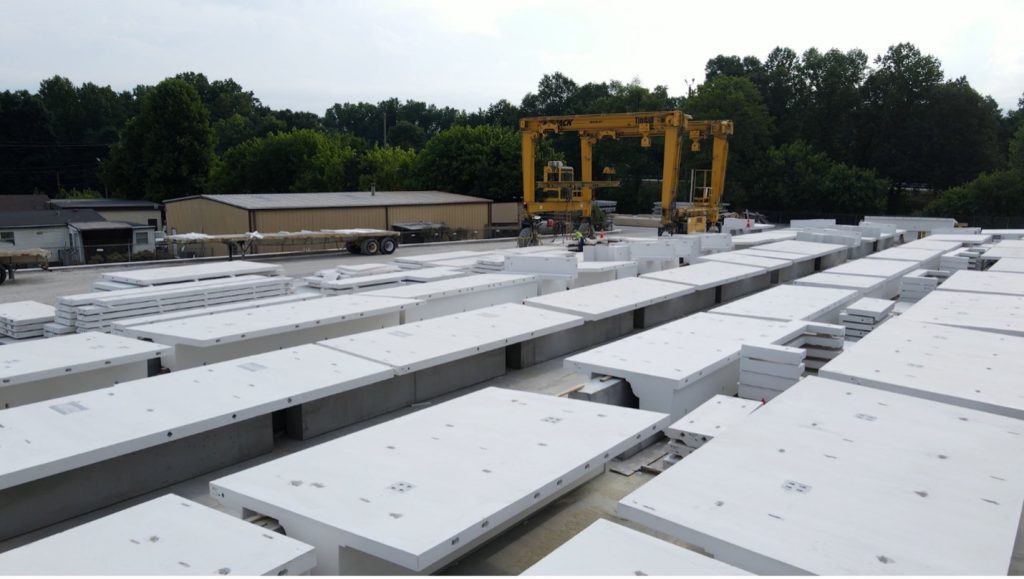
After the forming process is completed, the concrete, consisting of cement, aggregates, water, and additives, is poured into the molds. Once in place, the concrete is left to cure in a controlled environment, allowing it to develop optimal strength over the following twelve-hour period. When the concrete reaches the desired level of compressive strength, the precast elements are removed from the forms and then moved for additional finishing processes. This finishing includes surface treatments, sandblasting, and cleaning to enhance their aesthetic appeal. Once completed, the precast elements are then carefully transported to the construction site and prepared for installation.
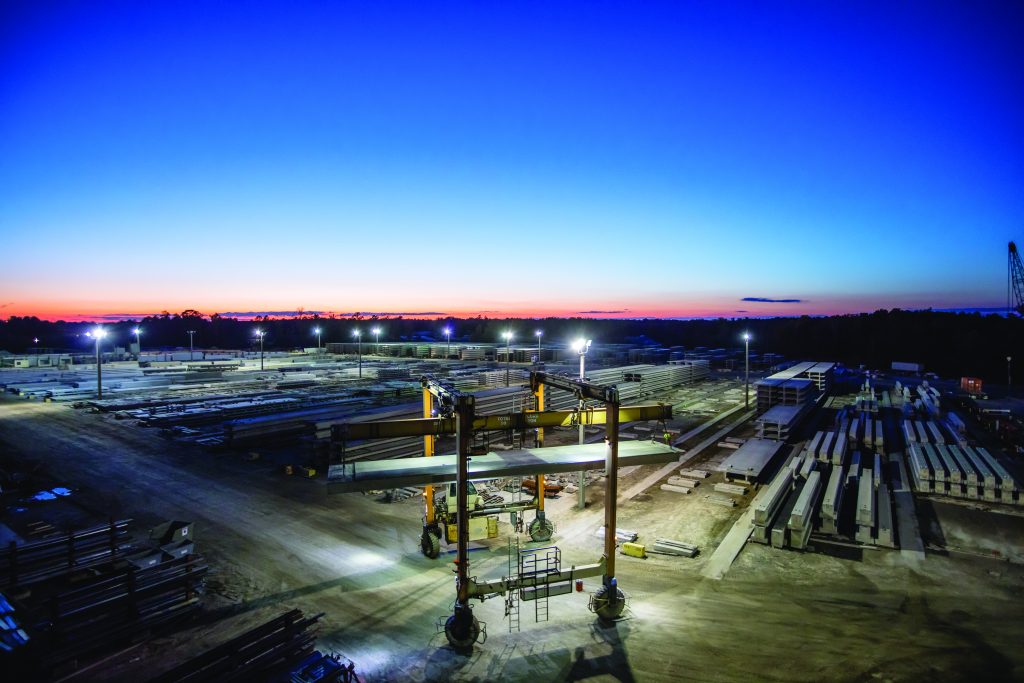
What Are the Applications of Precast?
While the term “precast concrete” may evoke images of straightforward, utilitarian construction, the versatility of precast is remarkable. It finds application in a wide range of project, including architectural facades, decorative elements, and structural components such as wall panels or floor slab systems like the Tindall Superior Lightweight All-Purpose Beam (T-SLAB®).
The true benefit of precast concrete lies in its design flexibility and structural efficiency. By utilizing form liners and architectural finishes, architects and engineers can create visually appealing and innovative structures without the constraints of traditional concrete construction. Precast elements are also capable of serving as the structure and building envelope, reducing the number of required materials and trades. Integration with other materials like steel, glass, or brick further expands the possibilities, allowing for the realization of unique architectural designs with unmatched durability. From 12-story multifamily apartment buildings to corporate headquarters expansions, precast can do it all.
What Are the Benefits of Precast?
The advantages of precast concrete are numerous. Firstly, the controlled manufacturing environment ensures superior quality control and precision, surpassing traditional concrete construction methods. This meticulous approach results in more consistent and reliable products. Secondly, precast elements can be manufactured concurrently with site preparation and foundation work, significantly reducing overall construction duration. Combined with the fact that precast concrete elements are ready for installation upon arrival at the job site, construction timelines can be accelerated, leading to substantial cost savings and faster project completion times. Third, the durability and resilience of precast concrete structures means lower maintenance and operating costs over the life of the building. Precast concrete buildings have a higher thermal mass than structures made primarily of wood or steel and typically are more energy efficient as a result. Because concrete has a larger mass than these materials, it can absorb and store heat. Since concrete reacts very slowly to changes in temperature, the heating and cooling loads are reduced, ensuring significant energy-cost savings over time. Non-metallic wythe connections cast within the panels can reduce or eliminate thermal bridges in the wall. Lastly, the dense composition of precast concrete wall panels is also an effective barrier against sound. The mass of concrete is particularly beneficial in providing sound transmission reduction. For noise-sensitive environments, precast building components are an ideal choice for creating quieter and more comfortable indoor environments.
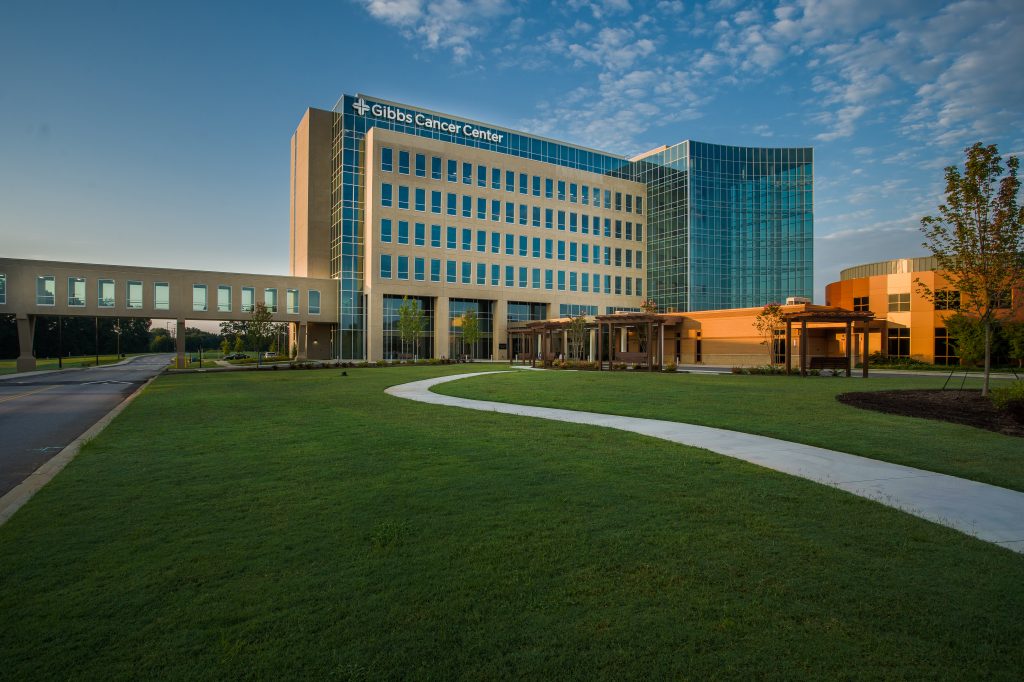
Conclusion
Precast concrete is a transformative construction material that offers a multitude of benefits. It not only delivers higher quality and more consistent results than traditional, cast-in-place concrete, but it also saves valuable time on the job site and provides unparalleled customization options. From architectural facades to structural elements, precast concrete opens doors to innovative designs and more efficient construction processes, making it suitable for any project.
At Tindall, we have devoted over 60 years to honing the precast process and establishing ourselves as industry leaders. We are committed to elevating your project to new heights by harnessing the power of precast . For more information about the advantages of precast construction and how Tindall can make a difference for you, contact our team today!